What is a solenoid valve?
A solenoid valve is an electromechanical device used to control the flow of fluids or gases. It consists of a solenoid coil, a movable plunger or piston, and a valve body with inlet and outlet ports.
Here's how a solenoid valve works:
1.Solenoid Coil: The solenoid valve has a coil of wire wound around a core. When an electric current is applied to the coil, it generates a magnetic field. Sometimes referred to as a bobine, electromagnet or solenoid actuator.
2. Plunger or Piston: Inside the solenoid coil, there is a movable plunger or piston connected to a sealing element. When the coil is energized, theArmature assembly magnetic field attracts the plunger or piston towards the coil. Sometimes referred to as a solenoid armature or solenoid poppet.
3. Valve Body and Ports: The valve body contains inlet and outlet ports that allow the fluid or gas to flow through the valve. The plunger or piston is positioned in such a way that it can open or close the flow path when activated.
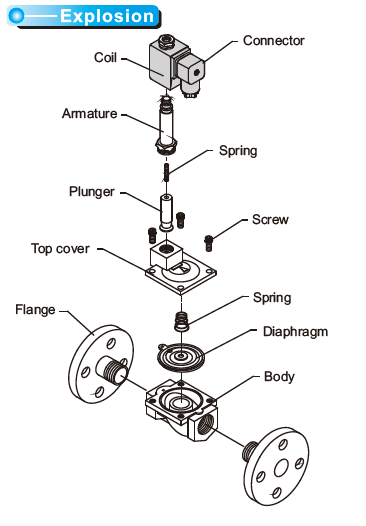
4. Flow Control: When the solenoid coil is energized, the plunger or piston is pulled towards the coil, which opens the valve and allows the fluid or gas to flow through. When the coil is de-energized, a spring or other mechanism returns the plunger or piston to its original position, closing the valve and stopping the flow.
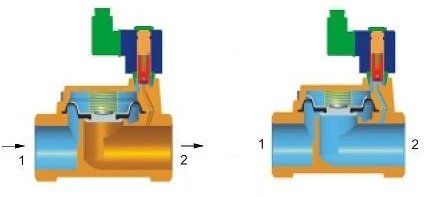
Solenoid valves are commonly used in a variety of applications, including:
- Industrial processes: Solenoid valves are widely used in manufacturing and industrial processes to control the flow of liquids or gases. They are used in applications such as controlling water, air, oil, steam, chemicals, and more.
- HVAC systems: Solenoid valves are used in heating, ventilation, and air conditioning (HVAC) systems to control the flow of refrigerants or air.
- Water and irrigation systems: Solenoid valves are used in water supply systems, irrigation systems, and sprinkler systems to control the flow of water.
- Automotive systems: Solenoid valves are found in various automotive systems, such as fuel systems, transmission systems, and emission control systems.
- Medical equipment: Solenoid valves are used in medical equipment, such as anesthesia machines, ventilators, and fluid control systems.
Solenoid valves offer quick and precise control over fluid or gas flow, and their operation can be automated by electrical signals. They are available in different configurations, such as two-way (on/off), three-way, and four-way valves, with various sizes, flow rates, and pressure ratings to suit different applications.
What is an ATEX solenoid valve?
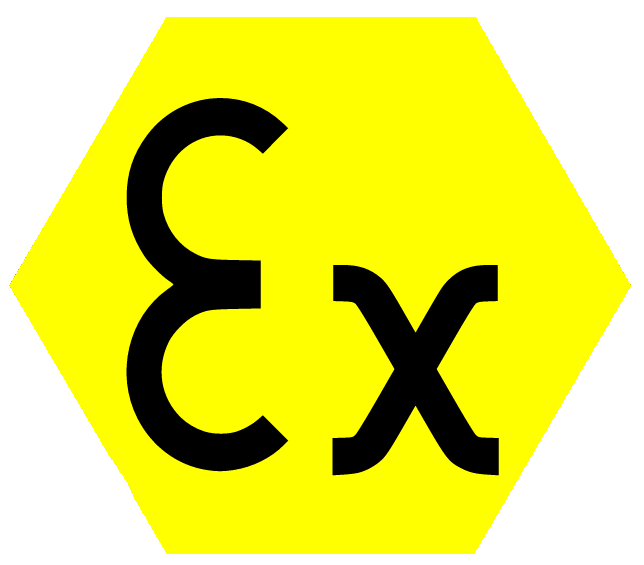
ATEX stands for "Atmosphres Explosibles," which is a European directive that deals with the control of explosive atmospheres and the equipment used in such environments. It is derived from two European directives:
1. ATEX Directive 2014/34/EU (also known as ATEX 114 or ATEX Equipment Directive): This directive covers the requirements for equipment and protective systems intended for use in potentially explosive atmospheres. It defines the obligations and responsibilities of manufacturers, importers, and distributors of equipment that is intended to be used in such environments.
2. ATEX Directive 1999/92/EC (also known as ATEX 137 or ATEX Workplace Directive): This directive focuses on the safety and protection of workers who work in potentially explosive atmospheres. It sets out the minimum requirements for the prevention of explosions, the protection of workers, and the overall safety management of workplaces where explosive atmospheres may occur.
The ATEX directives are applicable to various industries and sectors where explosive atmospheres can be present, such as chemical plants, oil refineries, gas processing facilities, mining operations, pharmaceutical manufacturing, and more.
Key aspects of ATEX include:
1. Classification of Explosive Atmospheres: ATEX provides guidelines for classifying hazardous areas into different zones based on the likelihood and duration of the presence of explosive atmospheres. These zones are classified as Zone 0, Zone 1, Zone 2 for gases, vapors, or mists, and Zone 20, Zone 21, Zone 22 for combustible dust.
2. Equipment and Protective Systems: The ATEX Equipment Directive (ATEX 114) establishes the requirements for equipment and protective systems that are intended for use in potentially explosive atmospheres. It sets out standards and conformity assessment procedures for ensuring that such equipment is designed, manufactured, and marked appropriately to meet the required safety standards.
3. Workplace Safety: The ATEX Workplace Directive (ATEX 137) focuses on the safety and protection of workers in potentially explosive atmospheres. It requires employers to carry out a risk assessment, implement suitable control measures, provide appropriate training to employees, and establish an explosion protection document.
4. Certification and Markings: Equipment that complies with the ATEX directives must undergo conformity assessment procedures, including testing and certification by notified bodies. Approved equipment is marked with the "CE" mark, followed by the Ex symbol and other relevant markings indicating compliance with specific standards and requirements.
Compliance with ATEX directives is essential for ensuring the safety of workers, preventing explosions, and mitigating the risks associated with explosive atmospheres. Businesses operating in hazardous environments need to adhere to ATEX requirements, including the use of appropriate equipment and implementing safety measures to protect their employees and facilities.
View all ATEX solenoid valves, Exm, Exd and Exia.
What is a direct acting solenoid valve?
A direct-acting solenoid valve, the solenoid coil directly controls the movement of the valve mechanism. When the solenoid coil is energized, it generates a magnetic field that attracts the plunger or piston, opening the valve and allowing the fluid or gas to flow. When the coil is de-energized, a spring or other mechanism returns the valve to its closed position, stopping the flow.
A direct acting solenoid valves is also known as a poppet valve, plunger type solenoid.
Direct-acting solenoid valves are typically used for applications that require fast, small compact solenoid valve with relatively low flow rates, tight sealing, high or low pressure or where there can be significant back pressure from spray nozzles.
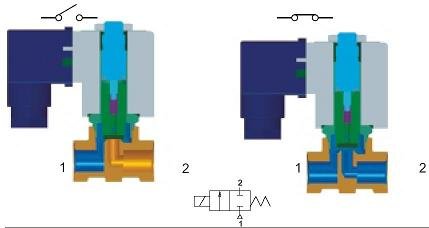
What is an assisted lift solenoid valve?
An assisted lift solenoid valve the diaphragm is mechanically linked to the plunger, so when the plunger is lifted by the electro-magnetic coil it also lifts the diaphragm to allow flow through the valve. Assisted lift is also known as kick pilot, hung diaphragm or zero rated solenoid valve.
Assisted lift solenoid valve is also known as a hung diaphragm valve, kick pilot valve, zero differential solenoid valve or coupled diaphragm solenoid valve.
Assisted lift solenoid valves are typically used for applications that require relatively high flow rates or where the pressure diffferential (ÎP) across the valve is relatively small. Typically the diaphragm will have an internal pilot that combines a pilot servo assist for higher system pressures. Note larger valves require bigger more powereful magnetic coils to mechanically lift the diaphragm.
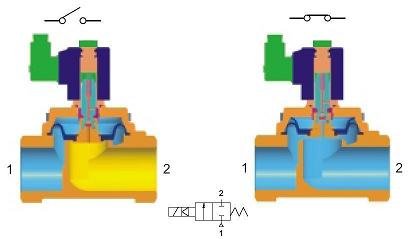
2. What is a pilot operated solenoid valve?
A pilot-operated solenoid valve, the solenoid coil controls a pilot mechanism, which in turn controls the flow of fluid or gas to the main valve. When the solenoid coil is energized, it opens the pilot mechanism, allowing pressure to act on a diaphragm or piston. The pressure differential (ÎP) across the diaphragm or piston then opens the main valve, allowing the fluid or gas to flow. When the solenoid coil is de-energized, the pilot mechanism closes, relieving pressure on the diaphragm or piston and allowing the main valve to close.
A pilot operated solenoid valve is also known as a floating diaphragm solenoid, servo solenoid valve, pressure assisted solenoid valve or media assisted solenoid valve.
Pilot-operated solenoid valves are commonly used in applications with higher flow rates or when there is a guarenteed minimum pressure differential across the valve, ideally between 0.5 Bar (7 psi) or at least 10% of the working pressure. By using a pilot mechanism, these valves can handle higher pressures and flow rates while requiring lower power consumption for operation.
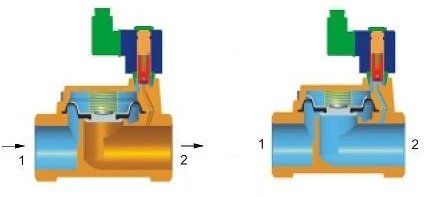
Key considerations when choosing between direct-acting and pilot-operated solenoid valves include the flow rate, pressure differential, power consumption, response time, and specific application requirements. Direct-acting valves are typically simpler and more economical for low-flow and low-pressure applications, while pilot-operated valves are suitable for high-flow and high-pressure applications that require precise control.
It's worth noting that there are variations and hybrid designs available, combining features of both direct-acting and pilot-operated solenoid valves to optimize performance for specific applications.
What is a high pressure solenoid valve?
A high-pressure solenoid valve is a type of solenoid valve designed specifically to handle and control fluids or gases under elevated pressure conditions. These valves are engineered to operate effectively and safely in systems where the pressure exceeds the capabilities of standard solenoid valves.
Key characteristics of a high-pressure solenoid valve include:
1. Pressure Rating: High-pressure solenoid valves are built to withstand and operate under high-pressure conditions. They have a higher pressure rating compared to standard solenoid valves. The pressure rating indicates the maximum pressure level that the valve can handle without leaks or failure.
2. Robust Construction: High-pressure solenoid valves are constructed using durable and robust materials, such as stainless steel or other high-strength alloys. These materials can withstand the forces exerted by high-pressure fluids or gases, ensuring the valve's integrity under demanding conditions.
3. Enhanced Sealing: Effective sealing is critical in high-pressure applications to prevent leaks and maintain system integrity. High-pressure solenoid valves employ advanced sealing mechanisms, such as high-quality gaskets, O-rings, or metal seals, that are specifically designed to withstand the elevated pressures and provide reliable sealing performance.
4. Reinforced Components: The components of high-pressure solenoid valves, such as the valve body, plunger or piston, and seals, are reinforced to handle the increased forces associated with high-pressure environments. These components are designed to withstand the stress and strain induced by the high-pressure fluid or gas flow.
5. Fast and Precise Operation: High-pressure solenoid valves offer rapid and accurate control over fluid or gas flow. When the solenoid coil is energized, it quickly opens or closes the valve, allowing for precise regulation of the flow rate. The fast response time ensures efficient operation in high-pressure systems.
6. Application Areas: High-pressure solenoid valves are commonly used in industries such as oil and gas, petrochemical, chemical processing, hydraulic systems, high-pressure water systems, and other applications that involve fluid or gas control under high pressure. They are employed in processes where reliable and precise control over high-pressure fluids or gases is required. It's important to note that the exact design and specifications of high-pressure solenoid valves can vary depending on the specific application requirements.
When selecting a high-pressure solenoid valve, it is essential to consider factors such as pressure rating, flow capacity, material compatibility, and environmental conditions to ensure optimal performance and safety.
View all high pressure solenoid valves.
What is a WRAS solenoid valve?
A WRAS solenoid valve refers to a type of solenoid valve that meets the requirements and standards set by the Water Regulations Advisory Scheme (WRAS) in the United Kingdom. WRAS is a regulatory body that promotes the protection of public health and the environment by ensuring the quality and safety of water supply systems.
WRAS certified solenoid valves are specifically designed and tested to comply with the regulations and guidelines outlined by WRAS. These valves are intended for use in applications involving the control or regulation of water supply, typically in plumbing, heating, or water treatment systems.
To obtain WRAS approval, solenoid valves undergo rigorous testing to assess their compliance with specific criteria related to material safety, performance, and water quality standards. This includes evaluating factors such as:
1. Material Compliance: WRAS solenoid valves must be manufactured using materials that meet the relevant standards for potable water applications, ensuring that they do not introduce harmful substances into the water supply.
2. Performance and Reliability: The valves are tested to ensure they perform reliably under specified operating conditions, including pressure, temperature, and flow rates. This ensures that they can effectively control the water supply while maintaining appropriate levels of safety and efficiency.
3. Water Quality: WRAS approved solenoid valves are assessed to ensure they do not have any adverse effects on water quality. They undergo tests to verify that they do not promote bacterial growth or contamination.
By using WRAS approved solenoid valves, installers and users can have confidence that the valves comply with the necessary regulations and standards, providing assurance of safety and water quality in their systems.
If you are considering using solenoid valves in a water supply system in the UK, it is recommended to check if WRAS approval is required and select valves that meet the appropriate WRAS standards for your specific application.
View all WRAS drinking water valves.
What is a 2/2 way normally closed Solenoid Valve?
A 2/2 way normally closed solenoid valve is a specific type of solenoid valve that controls the flow of fluids or gases in a system.
Let's break down its meaning:
1. 2/2 Way: The term "2/2 way" refers to the number of ports and positions the valve has. In this case, it means the valve has two ports (an inlet and an outlet) and two positions (open and closed).
2. Normally Closed: The term "normally closed" indicates the valve's default state when it is not energized. In a normally closed solenoid valve, the valve remains closed (shut-off) when no electrical power is applied to the solenoid coil. It only opens and allows flow when the solenoid coil is energized, creating a magnetic field that moves the valve mechanism to open the flow path.
In summary, a 2/2 way normally closed solenoid valve has two ports, with flow being blocked when the solenoid coil is not energized. It is commonly used in applications where it is necessary to shut off the flow by default and allow flow when the valve is energized.
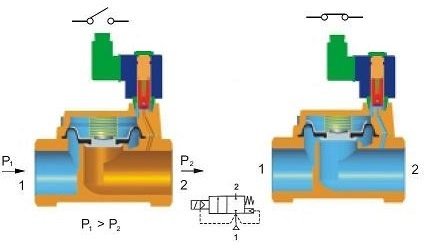
What is a 2/2 way normally open solenoid valve?
A 2/2 way normally open solenoid valve is a specific configuration of a solenoid valve that has two ports and two positions. Here's a breakdown of its characteristics:
1. Two Ports: A 2/2 way solenoid valve has two ports, often referred to as the inlet and outlet. These ports allow the flow of fluid or gas through the valve. One port serves as the inlet for the media, while the other port serves as the outlet.
2. Two Positions: The "2/2" designation signifies that the valve has two positions or states it can assume. In the case of a normally open solenoid valve, the two positions are as follows:
- Normally Open: The valve is in its default or de-energized state, where the flow path between the inlet and outlet ports is open. In this position, fluid or gas can flow through the valve freely.
- Actuated State: When the solenoid coil of the valve is energized, it changes the valve's position to close the flow path, interrupting the flow of fluid or gas through the valve.
3. Normally Open: In the case of a normally open solenoid valve, the valve remains open in its default or de-energized state. This means that when the solenoid coil is not energized, fluid or gas can flow through the valve without any obstruction. The valve only closes and stops the flow when the solenoid coil is energized.
Applications of a 2/2 way normally open solenoid valve can vary depending on the specific system requirements. They are commonly used in situations where it is necessary to control the flow of fluids or gases by interrupting the flow when the solenoid is activated.
It's important to note that solenoid valves come in various configurations, such as normally closed, normally open, and others, to suit different applications and system designs. The selection of the appropriate valve configuration depends on the specific needs and control requirements of the system.
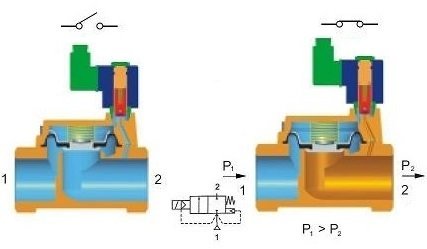
What is a 3/2 way solenoid valve.
A 3/2 way solenoid valve is a specific configuration of a solenoid valve that has three ports and two positions. Here's an overview of its 3/2 way solenoid valve manifold characteristics:
1. Three Ports: A 3/2 way solenoid valve has three ports, often referred to as the inlet, outlet, and exhaust ports. These ports determine the flow path of the fluid or gas through the valve. The inlet port is where the media enters the valve, the outlet port is where the media exits, and the exhaust port is used to release any pressure or fluid from the valve when it is in the deactivated state.
2. Two Positions: The "3/2" designation indicates that the valve has two positions or states it can assume. These positions are as follows:
- Deactivated State: In this state, fluid or gas flows from the inlet port to the outlet port, allowing for the normal flow through the valve. The exhaust port is closed, preventing any media from escaping.
- Activated State: When the solenoid coil of the valve is energized, it changes the valve's position, altering the flow path. In this state, the flow path between the inlet and outlet ports is closed, preventing the media from passing through the valve. At the same time, the exhaust port opens, allowing any media that was previously trapped in the valve to be released or redirected.
3. Functionality: A 3/2 way solenoid valve is commonly used for basic on/off control applications. It allows for the control and interruption of fluid or gas flow by switching between the activated and deactivated states. By energizing or de-energizing the solenoid coil, the valve can either enable or block the flow of media.
The specific application of a 3/2 way solenoid valve depends on the system requirements and the desired control functionality. They are widely used in various industries and applications, including pneumatic systems, fluid automation, process control, and more.
It's important to note that solenoid valves come in different configurations, such as 2/2 way, 3/2 way, 5/2 way, and others, each offering unique control capabilities and functions. The selection of the appropriate solenoid valve configuration depends on the specific needs and control requirements of the system.
View all 3/2 way solenoid valves.
What is a 5/2 way single acting solenoid valve
A 5/2 way single acting solenoid valve is a specific configuration of a solenoid valve that has five ports and two positions. Here's an overview of its characteristics:
1. Five Ports: A 5/2 way solenoid valve has five ports, often labeled as P, A, B, E, and S. These ports determine the flow path and control of the fluid or gas through the valve. The specific designation of the ports may vary depending on the manufacturer, but the general function remains the same.
- P Port (Pressure or Inlet Port): This is the port where the fluid or gas enters the valve from the pressure source.
- A and B Ports (Actuator Ports): These are the ports that connect to the actuator (e.g., cylinder or pneumatic device) that is being controlled by the valve.
- E Port (Exhaust Port): This port allows the release or exhaust of the fluid or gas from the actuator.
- S Port (Supply or Exhaust Supply Port): This port is used to supply or exhaust the control signal (compressed air or other media) to control the valve's positions.
2. Two Positions: The "5/2" designation signifies that the valve has two positions or states it can assume. These positions are as follows:
- Deactivated State (Normal Position): In this state, the valve routes the pressure from the P port to one of the actuator ports (A or B), while the other actuator port is connected to the exhaust port (E). This allows the actuator to move in one direction.
- Activated State: When the solenoid coil of the valve is energized, it changes the valve's position, reversing the flow path. In this state, the pressure is redirected to the other actuator port (A or B), while the previously connected actuator port is connected to the exhaust port (E). This allows the actuator to move in the opposite direction.
3. Single Acting: The term "single acting" refers to the type of actuation provided by the solenoid valve. In a single acting configuration, the valve controls the actuator movement in one direction (either extend or retract), while the actuator relies on other means, such as a spring or external force, to return to its original position.
The specific application of a 5/2 way single acting solenoid valve is typically found in pneumatic systems, where it is used to control the movement of pneumatic actuators, such as cylinders or valves. These valves are often used in applications requiring simple on/off control or directional control of pneumatic devices.
It's important to note that the specific arrangement and designation of the ports in a 5/2 way single acting solenoid valve may vary depending on the manufacturer or specific valve design. Therefore, it is recommended to consult the manufacturer's documentation or product specifications for accurate information regarding port designations and functionality.
View all 5/2 way mono stable solenoid valves.
What is a 5/2 way double acting solenoid valve.
A 5/2 way double-acting solenoid valve is a specific configuration of a solenoid valve that has five ports and two positions. Here's a breakdown of its characteristics:
1. Five Ports: A 5/2 way solenoid valve has five ports, often labelled as P (pressure), A (cylinder A), B (cylinder B), EA (exhaust A), and EB (exhaust B). These ports control the flow of fluid or compressed air in a pneumatic system.
2. Two Positions: The "5/2" designation indicates that the valve has two positions or states it can assume. These positions are as follows:
- Deactivated State: In this state, fluid or compressed air flows from the pressure port (P) to one of the cylinder ports (A or B) while the other cylinder port is connected to the corresponding exhaust port (EA or EB). This allows the actuator (such as a cylinder) to extend or retract depending on the flow path.
- Activated State: When the solenoid coil of the valve is energized, it changes the valve's position, reversing the flow path. The pressure port (P) is now connected to the other cylinder port (B or A) while the previously connected cylinder port is now connected to the corresponding exhaust port (EB or EA). This causes the actuator to move in the opposite direction, either retracting or extending, depending on the initial state.
3. Double Acting: The term "double-acting" refers to the actuation method of the valve. In a double-acting solenoid valve, both sides of the actuator (such as a pneumatic cylinder) can be pressurized and depressurized to achieve movement in both directions. By changing the position of the solenoid valve, the pressure is applied to one side of the actuator while the other side is exhausted, and vice versa.
4. Functionality: A 5/2 way double-acting solenoid valve is commonly used in pneumatic systems to control the movement of pneumatic actuators, such as cylinders or rotary actuators. By energizing or de-energizing the solenoid coil, the valve switches between the two positions, allowing for the actuation of the pneumatic device in both directions.
The specific application of a 5/2 way double-acting solenoid valve depends on the requirements of the pneumatic system and the desired control functionality. These valves are commonly found in various industrial automation applications, such as robotics, assembly lines, packaging machines, and more.
It's important to note that solenoid valves come in different configurations, each offering unique control capabilities and functions. The selection of the appropriate solenoid valve configuration depends on the specific needs and control requirements of the pneumatic system.
View all 5/2 way bi-stable solenoid valve.
What is a 5/3 way solenoid valve.
A 5/3 way double-acting solenoid valve is a specific configuration of a solenoid valve that has five ports, three positions, and operates using double-acting pneumatic actuators. Here's a breakdown of its characteristics:
1. Five Ports: A 5/3 way solenoid valve has five ports, typically labelled as A, B, P, R, and S:
- A and B ports: These are the two actuator ports. They connect to the double-acting pneumatic actuator to control its movement.
- P port: This is the pressure or supply port from where the pressurized fluid or gas enters the valve.
- R port: This is the exhaust or return port. It serves as the outlet for the fluid or gas when the actuator needs to release pressure.
- S port: This is the exhaust port for the opposite actuator. It allows the opposite actuator to exhaust air when the other actuator is pressurized.
2. Three Positions: The "5/3" designation indicates that the valve has three positions or states it can assume:
- Position 1: In this position, the P port is connected to the A port, allowing pressurized fluid or gas to flow to the actuator, causing it to move in one direction. The B port is connected to the R port, providing an exhaust path for the opposite actuator.
- Position 2: In this position, the A port is connected to the R port, allowing the actuator to release pressure and move in the opposite direction. The P port is blocked, cutting off the supply of fluid or gas.
- Position 3: In this position, the B port is connected to the P port, enabling the actuator to move back in the initial direction. The R port is connected to the S port, providing an exhaust path for the opposite actuator.
3. Double-Acting: The term "double-acting" refers to the type of actuator used in conjunction with the solenoid valve. A double-acting pneumatic actuator requires air pressure to move in both directions. The 5/3 way solenoid valve provides the necessary control of the actuator's movement by supplying and exhausting air from the appropriate ports.
A 5/3 way double-acting solenoid valve is commonly used in pneumatic systems that require precise control over the movement of double-acting actuators, such as cylinders or rotary actuators. They find applications in industries such as manufacturing, automation, and robotics, where precise actuation and control are necessary.
It's important to note that solenoid valves come in various configurations, each with its specific port, position, and actuation characteristics. The selection of the appropriate solenoid valve depends on the requirements of the pneumatic system and the desired control functionality.
View all 5/3 way solenoid valves.
What is a latching solenoid valve.
A latching solenoid valve is a type of solenoid valve that utilizes a magnetic latching mechanism to maintain its position without continuous electrical power. Unlike conventional solenoid valves that require a constant power supply to stay open or closed, latching solenoid valves have a unique design that allows them to hold their position even when the power is removed.
Here's how a latching solenoid valve typically operates:
1. Magnetic Latching Mechanism: A latching solenoid valve incorporates a permanent magnet within its structure, along with two opposing coils or windings. The permanent magnet holds the valve in a specific position when the coils are not energized.
2. Position Maintenance: When an electrical pulse is applied to one of the coils, it generates a magnetic field that opposes the magnetic field of the permanent magnet. This counteracting force causes the valve to switch to the opposite position.
3. Latched Position: Once the valve has switched to the desired position, the electrical power can be removed. The permanent magnet maintains the magnetic force required to keep the valve in its new position, even without electrical power. This means the latching solenoid valve remains in its current state until a subsequent electrical pulse is applied to the opposing coil to switch its position.
Latching solenoid valves are commonly used in applications where power consumption needs to be minimized or when maintaining valve position during power outages or failures is crucial. They can be found in various industries, including irrigation systems, fluid control, HVAC (heating, ventilation, and air conditioning), and other automated systems.
It's important to note that latching solenoid valves may have specific electrical requirements and operational considerations. It's essential to follow the manufacturer's guidelines and specifications for proper installation and operation of the valve.
View all latching solenoid valve.
What is a gas solenoid valve.
A gas EN161 solenoid valve refers to a specific type of solenoid valve that complies with the EN161 European standard for gas safety valves. The EN161 standard sets requirements for safety and performance for valves used in gas appliances and installations.
Here are some key features and requirements of a gas EN161 solenoid valve:
1. Safety Compliance: Gas EN161 solenoid valves are designed to meet specific safety standards to ensure the safe control of gas flow in various applications. These valves undergo rigorous testing and certification processes to ensure they comply with the requirements of the EN161 standard.
2. Functionality: Gas EN161 solenoid valves typically have a normally closed configuration, meaning that the valve remains closed in its default state, and gas flow is interrupted. When energized by an electrical signal, the valve opens, allowing gas to flow through the valve. This configuration provides a safety mechanism to shut off the gas supply in the event of power failure or other emergencies.
3. Performance and Reliability: EN161 solenoid valves are designed to provide reliable and consistent performance in gas applications. They are expected to meet specific criteria related to pressure ratings, flow rates, response times, and leakage rates. These requirements ensure that the valves operate efficiently and safely within the specified parameters.
4. Installation Considerations: Gas EN161 solenoid valves may have specific installation requirements and guidelines. These guidelines typically cover aspects such as proper orientation, electrical connections, pressure ratings, and the compatibility of the valve with the gas being controlled. It is essential to follow the manufacturer's instructions and any relevant national or local regulations during installation.
Gas EN161 solenoid valves are commonly used in various gas-related applications, including heating systems, industrial processes, commercial kitchens, and other installations where the controlled flow of gas is critical. They play a crucial role in ensuring the safe and reliable operation of gas appliances and systems.
When considering the use of a gas EN161 solenoid valve, it is important to verify that the specific valve you are considering meets the EN161 standard and is suitable for your intended application.
What is a motor actuated ball valve.
A 2-way motor actuated ball valve is a type of valve that is controlled by a motor and has two ports for fluid or gas flow. Here's an overview of its characteristics:
1. Two Ports: A 2-way motor actuated ball valve consists of two ports, commonly referred to as the inlet and outlet. These ports determine the flow path of the fluid or gas through the valve. The valve can either allow or block the flow by rotating the ball inside the valve body.
2. Motor Actuation: The valve is operated by an electric or pneumatic motor. The motor provides the necessary torque to rotate the ball within the valve body, thereby controlling the flow of the media. When the motor is activated, it rotates the ball to either open or close the valve, allowing or stopping the flow through the ports.
3. Ball Valve Design: The 2-way motor actuated valve utilizes a ball with a hole or bore in the center. When the valve is open, the ball is aligned with the flow path, allowing fluid or gas to pass through. When the valve is closed, the ball is rotated to block the flow, sealing off the ports.
4. Control and Automation: Motor actuated ball valves are commonly used in automated systems where precise control over the flow is required. They can be integrated into process control systems, HVAC (heating, ventilation, and air conditioning) systems, industrial applications, and other situations where remote or automatic operation is desired.
Motor actuated ball valves offer several advantages, including quick response times, accurate flow control, and the ability to integrate with control systems for remote operation and monitoring.
When selecting a 2-way motor actuated ball valve, it is important to consider factors such as the size, material compatibility, pressure and temperature ratings, voltage requirements, and the type of motor actuation (electric or pneumatic) that best suits your specific application and system requirements.